Introduction
When it comes to solutions about bulk storage, the range of options is vast. There are many good technical solutions available on the silos and tanks market. The choice of material, the location and sizing are fundamental questions for this first stage in the production process of baking industry products: Bread, pastries, cakes, biscuits, and all related products made with dry powdered raw materials such as flour, sugar, and salt.
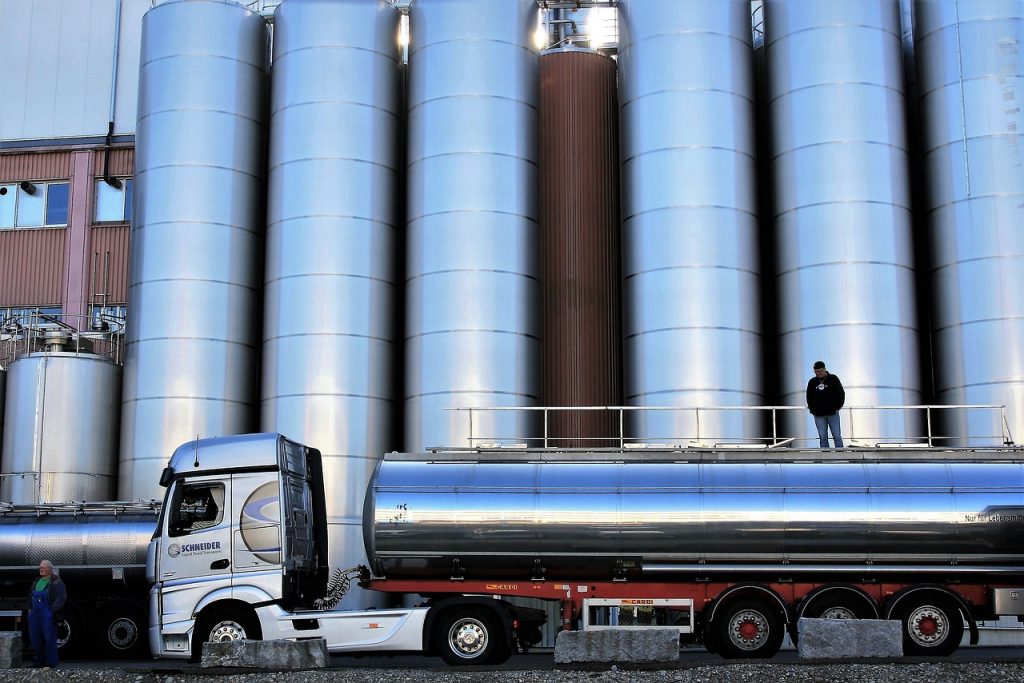
If you’re looking for bulk storage solutions for your baking industry ingredients, you will figure out that the options are numerous and varied. But which one meets your needs? A technical solution may seem relevant but could quickly to turn out to be a poor choice. This is the foundation of Hopi Consulting support: understanding your needs and finding THE technical solution that matches YOUR needs.
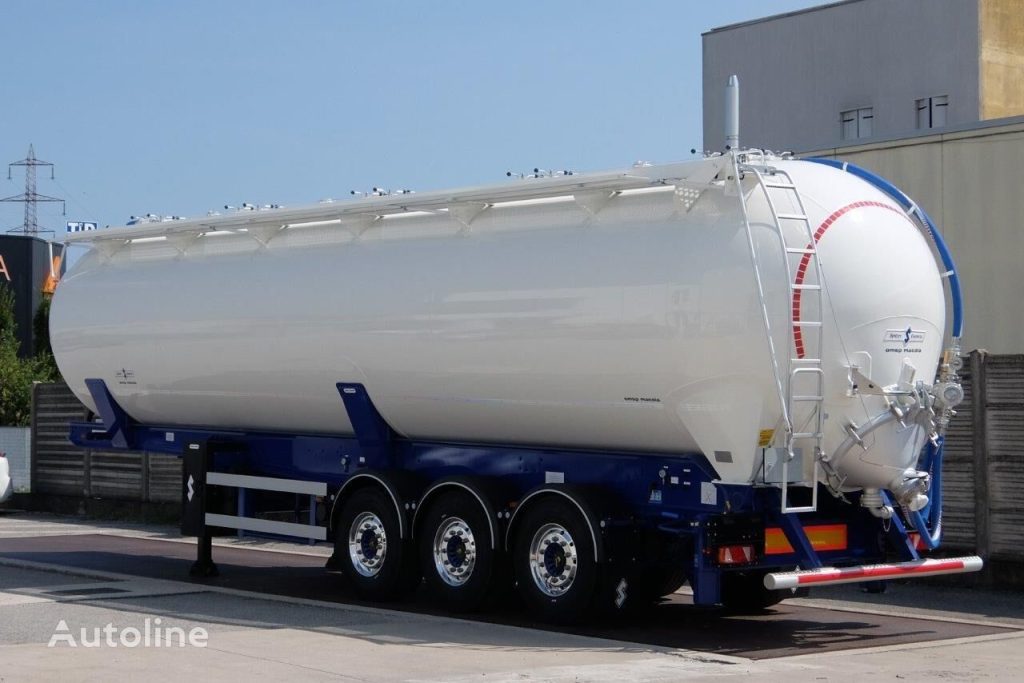
Technical solutions
What king of material ? Stainless steel or not ?
Stainless steel? Aluminum? Polyester resin? Once again, all of these choices make sense when aligned with economic objectives, quality expectations, and constraints. Stainless steel is the best option if the consideration of food safety for components is a high priority, but it is often the most expensive choice. On the other hand, materials like aluminum or polyester are generally more cost-effective without being inappropiate regarding food safety. Therefore, there are no bad choices as long as they match your sensitivity to the “Quality” aspect and are consistent with your budget.
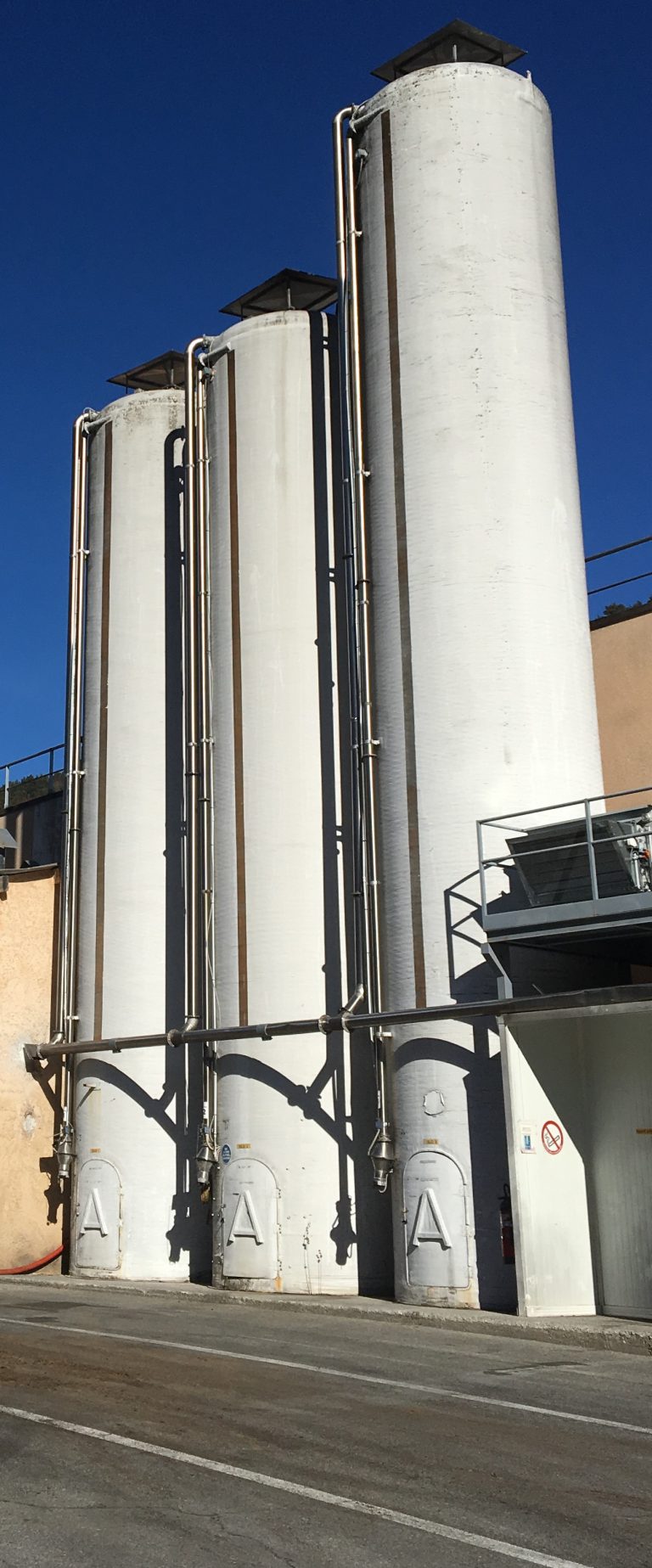
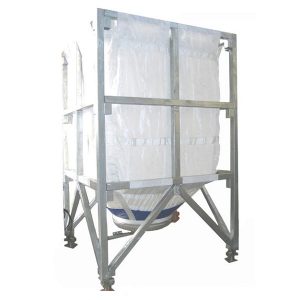
And what about flexible silos? Of course, these silos, made of a metal structure supporting an anti-static, high tenacity, woven polyester skin. Supporters of this solution appreciate the ventilation it allows for flour through the silo. Other advantages include cost, ease of transportation and assembly, and easier cleaning. However, these silos must be installed in a building designed for that purpose.
What about the location of bulk silos ?
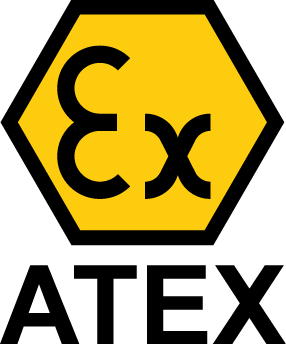
Indoors or outdoors? Or maybe the best solution is simply having a roof above the outdoors silos? Again, each option has its advantages depending on your needs and circumstances. Indoor silos are more expensive as they require built space, but this choice guarantees that the equipment stays dry and protected from the elements. It also provides more secure access for technicians. However, this decision demand more administrative procedure as it may require a construction permit in the case of a new building dedicated to silos. Beware of dust confinement in this building, which increases ATEX risk.
On the other hand, outdoor silos require more careful consideration regarding orientation, as positioning them directly south is to be avoided due to unwanted sun condensation effects. Options like insulation (double-jacket insulation or the creation of heating or cooling circuits) become viable solutions. Access to the top of silos is a key element to define for outdoor silos, and traditional caged ladders can now be replaced by thoughtful access points from the upper parts of the factory building roof space. In conclusion, these issues are complex and deserve detailed study. By considering all the benefits and constraints, the best choice can be made.
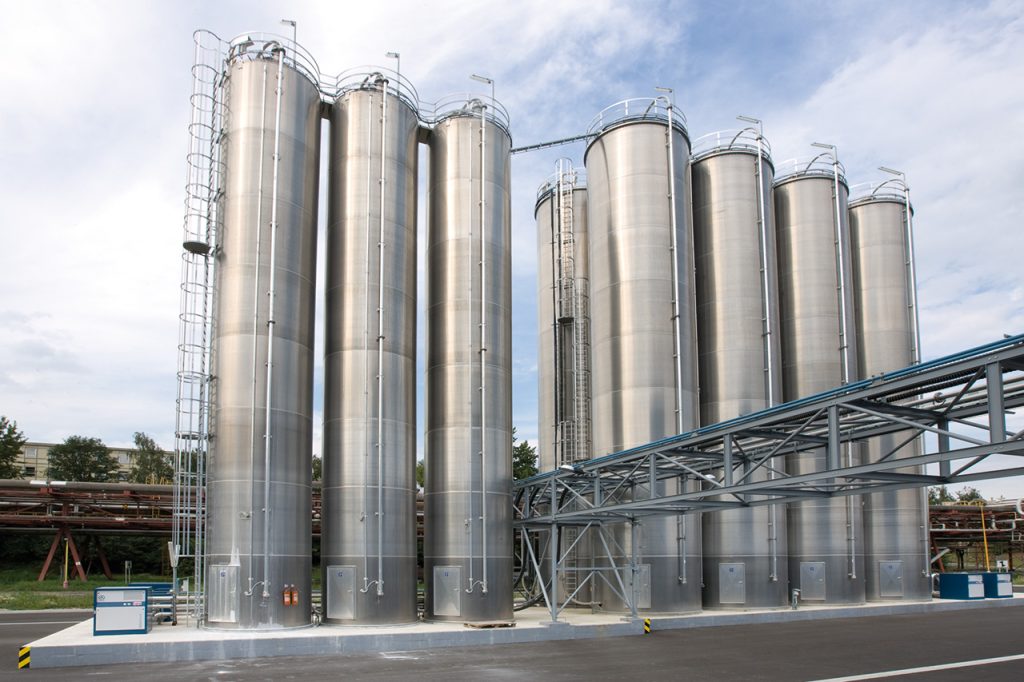
Which size ? Wich capacity ?
I repeat, but once again, sizing a silo for just one tanker or for storing the accumulation of two or three trucks brings advantages and disadvantages that only you can decide on. Consideration of traceability and the mixing of different raw material batches will guide your choices: the desire (or not) to empty completely to create zero-level point, trust in weighing solutions on load cells, and automatic discharge systems that preserve FIFO (First In, First Out). Wanting large storage capacity for comfortable stock management is not the same as having multiple dedicated and specific ones. In any case, I advise not to choose a silo that is too large, which could lead to insufficient movement of your raw material.
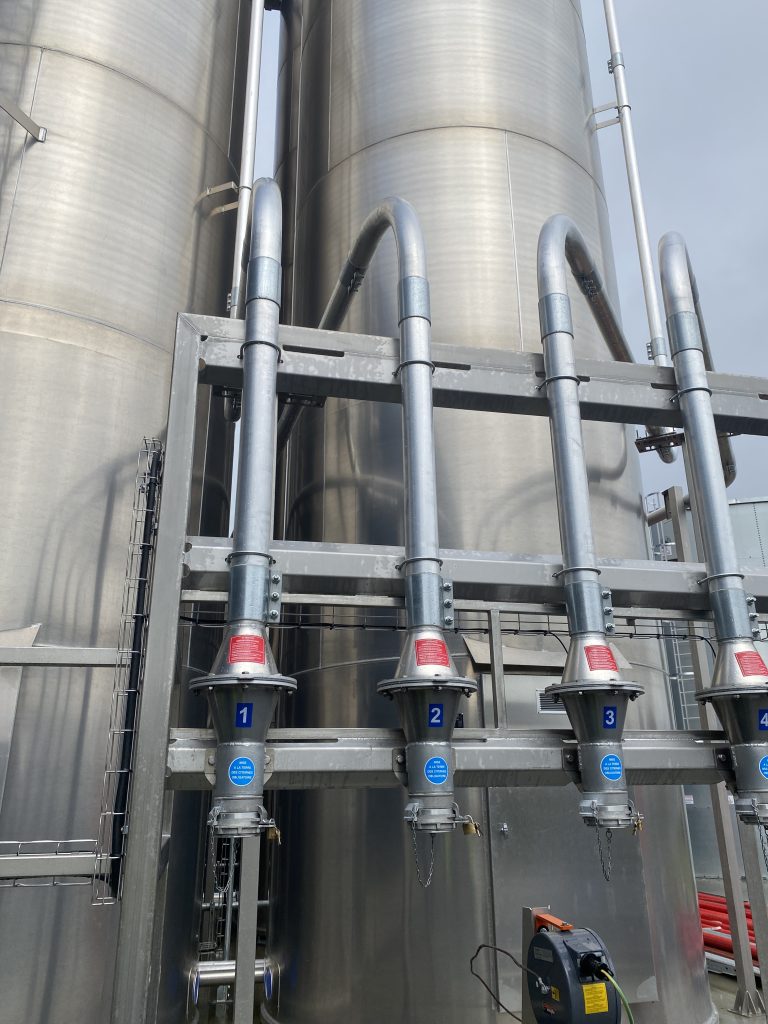
What about sugar and salt ?
Should sugar or salt be considered more specifically than flour? Definitely yes, due to hygroscopic issues. The extraction step cannot contain the effects of clumping. Therefore, it is essential to associate an air treatment system through drying and dedicated extraction equipment to manage these risks.
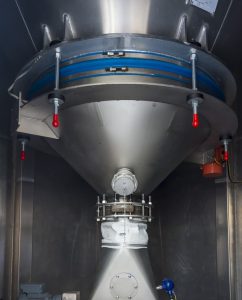
Conclusion
If you want to make the right choice for silos for your dry ingredients used in bread, pastries, cakes, and other baking industry products, don’t consider the silo as a simple container. Instead, give the appropriate level of consideration to the additional options that come with it: particularly air filtration and the extraction system. And why not integrate a pressurization system specific to the silo to eliminate the risk of pressure surges from tanker trucks? And why not dry the pressurized air to control moisture risks in your silo? Let’s talk about it together…
This article was written by Hopi Consulting, engineering dedicated to the baking industry.
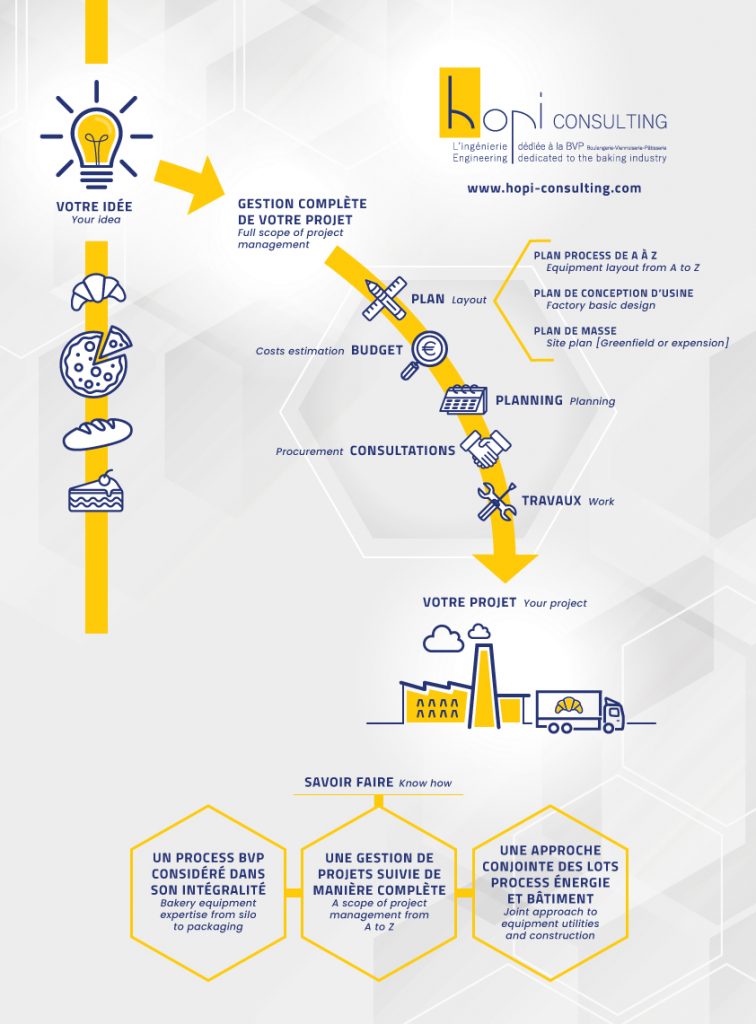